Порошок Si3N4 является основным сырьем для изготовления шариков из нитрида кремния . Выбор подходящего метода обработки для получения порошка правильной формы и равномерного распределения частиц по размерам является основой стабильного осуществления процессов формования, спекания, обработки и других процессов керамических шариков Si3N4.
В соответствии с различными методами распыления методы распылительной грануляции порошка Si3N4 в основном включают центробежную грануляцию распылением, грануляцию распылением под давлением и двухжидкостную грануляцию распылением. Грануляция распылением под давлением. Взвесь с однородным порошком Si3N4 распыляется в грануляционную колонну под высоким давлением для распыления, а капли быстро высушиваются в сферический порошок потоком горячего воздуха, что может предотвратить агломерацию и седиментацию различных компонентов в суспензии. Контролируя скорость испарения растворителя на поверхности частиц, можно получить правильную морфологию частиц и упаковать порошок для распылительной грануляции с равномерным распределением частиц по размерам, хорошей текучестью и подходящей свободной плотностью. Таким образом, производительность формы для наполнения порошка улучшается, а плотность и однородность заготовки увеличиваются. Поэтому для изучения влияния сыпучей плотности порошка распылительной грануляции на свойства керамических шариков Si3N4 был выбран метод грануляции распылением под давлением.
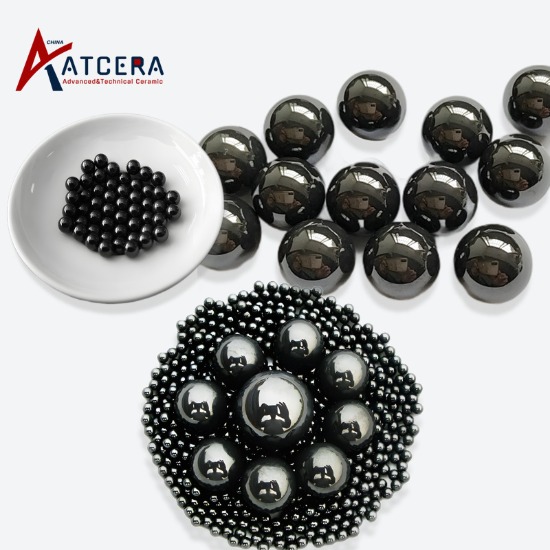
Испытательный материал
Порошок Si3N4 (при совокупной объемной доле в гранулометрическом составе 50%, соответствующий размер частиц D50=1,5 мкм, содержание α-Si3N4 93%, чистота 99,9%), порошок Y2O3 (D50=1,8 мкм, чистота 99,9%), порошок Al2O3 (D50=2,2 мкм, чистота 99,95%) и т.д.
Подготовка проб
Согласно массовому соотношению Si3N4-Y2O3-Al2O3= 92%-4%-4%, смесь добавляли в шаровую мельницу, в качестве растворителя использовали безводный этанол, в качестве растворителя использовали шар Si3N4. мелющая среда для смешивания и диспергирования, время смешивания составляло 24 часа, массовое соотношение шариков Si3N4 и смешанного порошка составляло 3:1. После равномерного перемешивания массовая доля твердой фазы суспензии составляет 55%, а вязкость — 4000 МПа·с. Контролируя температуру на входе в башню распылительной сушки и диаметр распылительной пластины, получали гранулированный порошок с различной сыпучей плотностью. Порошок Si3N4 для распылительной грануляции был спрессован в керамическую таблетку диаметром 8,731 мм с помощью сухого пресса, а затем было проведено спекание под атмосферным давлением при 1850°С, скорость нагрева составляла 3°/мин, время выдержки составляло 1,5 часа, давление азота 9 МПа. Свойства были проверены после приготовления.
Результат
Данные о фракции просеивания и сыпучей плотности гранулированного порошка, полученного различными способами распылительной грануляции с использованием одной и той же суспензии, показаны в таблице 1. Плотность заготовки керамических гранул, плотность спекания, прочность на изгиб, нагрузка на раздавливание, вязкость разрушения и твердость по Виккерсу Керамические гранулы, спрессованные порошком распылительной грануляции с различной насыпной плотностью, показаны в Таблице 2.
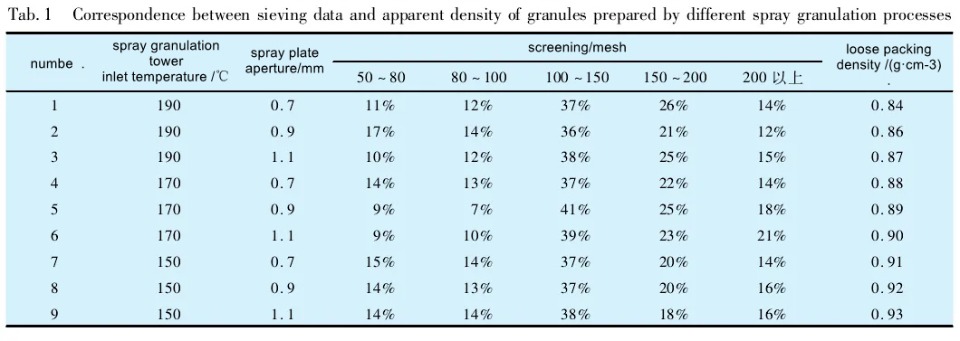
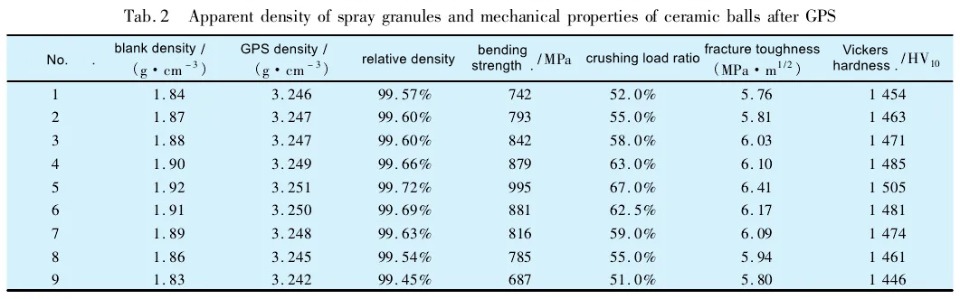
Механические свойства керамического шарика Si3N4, спрессованного гранулированным порошком 5#, являются лучшими. Слишком высокая или слишком низкая свободная плотность повлияет на эффективность прессования порошка и плотность заготовок керамических шариков Si3N4, тем самым влияя на механические свойства керамических шариков Si3N4. Механизм заключается в том, что рыхлая плотность напрямую влияет на пористость порошка распылительной грануляции после прессования, а газ трудно выпустить, что приводит к большому расстоянию миграции частиц и веществ во время процесса спекания, что не способствует уплотнению спекания.
Морфология частиц порошка 5# Si3N4, полученного методом распылительной грануляции, твердая и сферическая (рис. 1).
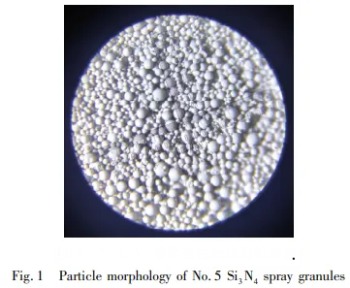
Микроструктура керамического шарика Si3N4 GPS, полученного порошком распылительной грануляции 1# ~ 9#, показана на рисунке 2. С увеличением рыхлой плотности грануляционного порошка количество пор внутри керамического шара Si3N4 после GPS сначала увеличивается, а затем уменьшается. , а плотность керамического шарика Si3N4 сначала увеличивается, а затем уменьшается.
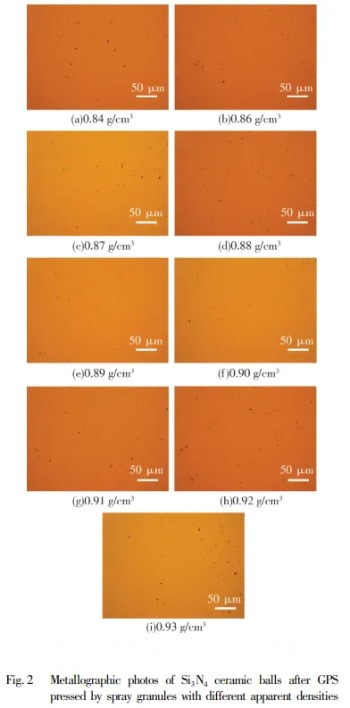
СЭМ использовался для наблюдения за микроструктурой и морфологией изломов зерен измельченных образцов керамических шариков Si3N4 с лучшими механическими свойствами и плохими механическими свойствами. Как показано на рисунке 3, плотность керамических шариков Si3N4 сначала увеличивалась, а затем уменьшалась с увеличением сыпучей плотности гранулированного порошка. Слишком высокая или слишком низкая сыпучая плотность приведет к неравномерному росту зерен и образованию внутренних пор.
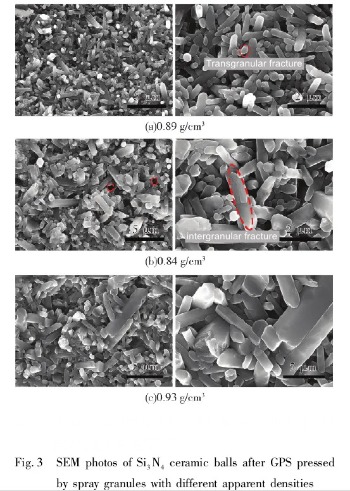
Заключение
Используя порошок Si3N4 в качестве сырья и Y2O3 и Al2O3 в качестве спекающих добавок, было проанализировано влияние сыпучей плотности порошка распылительной грануляции на уплотнение и механические свойства спекания керамических шаров. Были сделаны следующие выводы:
1) Плотность керамической заготовки шара Si3N4 сначала увеличивается, а затем снижается с увеличением насыпной плотности гранулированного порошка. При плотности свободной упаковки 0,89 г/см3 керамический шарик Si3N4 имеет самую высокую степень уплотнения и лучшие механические свойства.
2) Когда объемная плотность порошка распылительной грануляции составляет 0,89 г/см3, сформированный керамический шарик Si3N4 имеет наименьшие поры, однородный размер зерна и в основном принимает режим трансгранулярного разрушения.