Подложка из карбида кремния, как новое поколение полупроводниковых продуктов, продемонстрировала большой потенциал применения в области силовой электронной техники благодаря своим превосходным физическим и химическим свойствам. Однако высокая эффективность и малые потери при резке слитков SiC являются одной из ключевых технологий, ограничивающих его массовое производство. В настоящее время резка минометной проволокой и резка алмазной проволокой являются двумя основными технологиями резки слитков SiC, и они имеют существенные различия в способах введения абразива, эффективности обработки, потерях материала и воздействии на окружающую среду. Целью этой статьи является сравнение и анализ характеристик этих двух технологий резки, а также обсуждение направлений оптимизации процесса резки SiC.
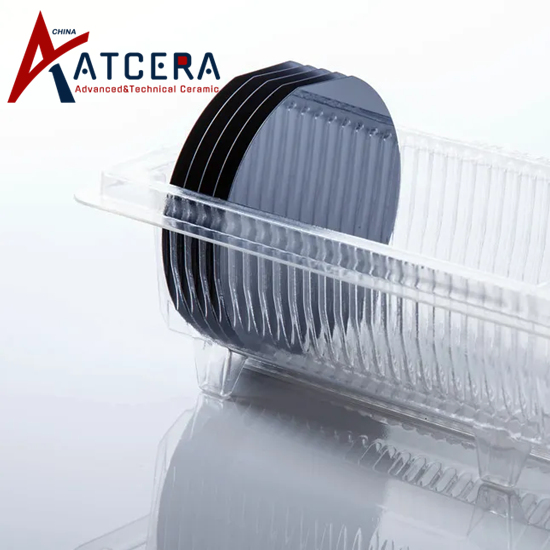
1. Режим импорта абразива и эффективность обработки
· резка растворной проволокой: при использовании свободного абразива скорость обработки относительно низкая.
· резка алмазной проволокой: посредством гальванопокрытия, связывания смолой и других методов фиксации абразивных частиц скорость резки увеличивается более чем в 5 раз, что значительно повышает эффективность производства.
2. Потери материала и скорость выхода пленки
· резка растворной проволоки: низкая производительность, большие потери материала.
· резка алмазным канатом: производительность увеличивается на 15–20%, потери материала значительно сокращаются, а экономическая выгода увеличивается.
3. Преимущества защиты окружающей среды
· Резка алмазным канатом: меньше отходов и сточных вод, более экологично.
4. Технические проблемы и стратегии их решения
· Резка алмазным канатом: существуют проблемы с контролем кристаллов и контролем потерь при резке.
· Стратегия решения проблем: В настоящее время в отрасли применяется стратегия резки минометной проволокой в качестве основной и резка алмазной проволокой в качестве вспомогательной, соотношение использования составляет около 5:1. В будущем необходимо дальнейшая оптимизация технологии резки алмазным канатом, чтобы повысить ее конкурентоспособность при резке SiC.
5. Анализ потерь при обработке материалов SiC
· потери при резке минометной проволоки:
· Потери на надрезе: до 150-200 микрон.
· Потери полировки: Повреждения поверхности необходимо устранять путем грубого шлифования, тонкого шлифования и процессов CMP.
· потери при обратном утончении: первоначальная настройка толщины высока, для уменьшения сопротивления требуется обратное утончение.
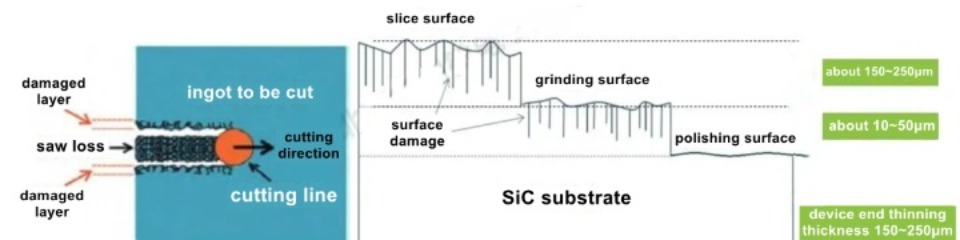
Потери и повреждения при резке SiC
Подводя итог, можно сказать, что технология резки алмазным канатом при резке слитков SiC демонстрирует значительные преимущества в скорости обработки, меньшие потери материала и преимущества в защите окружающей среды, но ее контроль над кристаллами и контроль потерь при резке все еще нуждаются в дальнейшей оптимизации. В настоящее время стратегия взаимодополняющего использования резки растворной проволокой и резки алмазной проволокой является обычной практикой в отрасли. Ожидается, что в будущем, благодаря постоянному развитию технологии резки алмазным канатом и снижению затрат, она займет доминирующее положение в области резки SiC. В то же время, ввиду проблемы потерь при обработке материалов SiC, необходимо дальнейшее изучение более эффективных процессов резки и полировки с низкими потерями, чтобы способствовать эффективному и недорогому производству полупроводниковых материалов SiC и продвигать его. широкое применение в области силовой электронной техники.